Laser Cutting: Pros vs Cons
Efficiency Meets Precision
One of the most important developments in recent history for the metal fabrication and manufacturing industry has definitely been the introduction of laser cutting. The combination of automated computer-controlled precision with accurate cutting ability has been crucial in furthering todays fabrication industry. Not only has it expanded cutting capabilities, but also created new efficiencies. But what are the pros and cons of this particular process, and how can they help you produce a quality product efficiently and with precision? First off we will look at the pros, starting with:
Efficiency and Material Savings
Due to the application of lasers, the entire manufacturing process has become more cost effective and environmentally friendly. Introduction of CAD drawings to program today’s laser cutters has been a massive help in reducing waste and increasing efficiency. Being computer controlled not only allows precision cutting with a very low error rate. It can also operate at a much higher rate of speed than other cutting technologies especially when making intricate cuts. All of this is done with a low labor requirement and practically no manual labor. These increased manufacturing efficiencies, increased speed, reduced waste and low labor requirements, lead to increased production at a lower production cost.
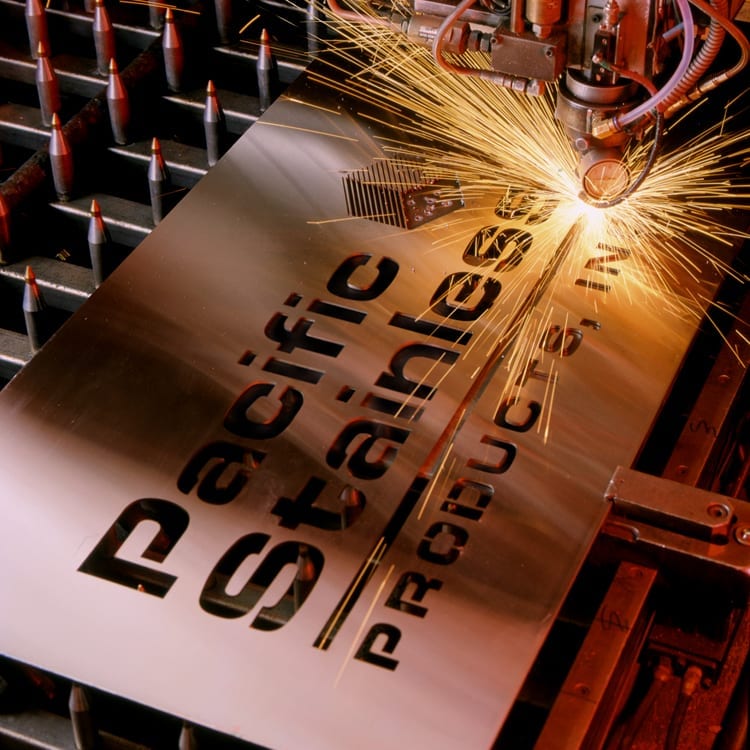
Versatility and Ease of Assembly
One of the major pros of laser cutting is the ability to make ready to weld components all in one complete process. The laser is capable of creating a burr free edge to a precise measurement. Negating the time and labor that would otherwise be used on grinding or finishing the edge before welding. And because of the functionality of the laser, all of these cuts can be completed on the component in one end to end procedure rather than multiple jobs.
Very Small Heat Affected Zone (HAZ)
The heat affected zone is the area of the steel where the intense heat from the cutting source has caused changes in the steel itself. The rapid fluctuation in temperature can cause nitriding, oxidation, and hardening which can also make the metal more brittle. The laser however, focuses its beam into a very small surface area reducing the heat affected zone significantly when compared to other cutting technologies such as oxyfuel or plasma.
Precision and Repeatability
As previously mentioned, the use of CAD drawings and assembly programming to program laser cutting has made for a reliably precise process. But unlike other cutting tech, lasers allow for much more design freedom and are able to follow much more intricate plans. Many laser setups function in a 3D environment allowing for the creation of angled edges, teeth, or various interlocks to create a stronger joint and make for an easier welding process. Additionally, since the laser is a contactless cutting medium it doesn’t weaken the metal unlike a physical penetration such as a punch or saw.
Although there are many pros when it comes to using laser cutting in a metal manufacturing environment. There are still some cons:
Specialist Training
Although the laser cutting process requires relatively little manual labor, there is still the need for a trained specialist to run the system and input the plans. The specialist may require specific certifications in addition to on the job experience in order to make the most of the laser cutters potential. In addition an experienced operator will be familiar with the limitations of the system.
Metal Thickness Limitations
Metal thickness has a large influence on efficiency when it comes to laser cutting. Some other cutting technologies have a tendency to be more suited for thick cuts. Our sheet metal laser will make stainless steel cuts up to ½ inch and steel cuts up to an inch thick. Cutting ability is not only affected by thickness but also by reflectivity. Copper, bronze, and aluminum are more difficult to cut and, in some cases impossible depending on the machine being used. Fiber lasers have a tendency to be more capable when cutting more reflective surfaces than CO2 lasers.
When it comes to metal fabrication and manufacturing, lasers have become the gold standard. Their precision, efficiency, speed, and versatility result in not only cost savings across the board, but also a better, stronger overall product. Their automation has made it so that even if you are doing a multiple unit production run, the products fit and quality will be identical. Is a laser cut the preferred method for your product?
Call Us Today:
(888) 618-2122
